C. Pengkutuban Elektroda
1. Pengkutuban Langsung
Pada pengkutuban langsung ini, kabel elektroda dipasang pada terminal negative (-) dan kabel massa pada terminal positif (+). Pengkutuban langsung sering disebutserkuit las listrik dengan elektroda negative (DC ¯ ).
2. Pengkutuban Terbalik
Untuk pengkutuban terbalik, kabel elektroda dipasang pada terminal positif dan kabel massa dipasang pada terminal negative. Pengkutuban terbalik sering disebut sirkuit las listrik elektroda positif (DC+).
3. Pengaruh Pengkutuban Pada Hasil Las
Pemilihan jenis arus maupun pengkutuban pada pengelasan tergantung kepada :
a. Jenis bahan dasar yang akan dilas
b. Jenis elektroda yang dipergunakan
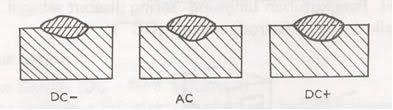
Pengaruh pengkutuban pada hasil las adalah pada penembusan lasnya. Pengkutuban langsung akan menghasilkan penembusan yang dangkal, pengkutuban terbalik akan menghasilkan penembusan yang dalam. Pada arus bolak-balik (AC), penembusan yang menghasilkan dapat dangkal dan dapat dalam, atau antara keduanya.
PERALATAN LAS LISTRIK
Peralatan las listrik ini terdiri dari :
a. Pesawat las,
b. Alat-alat bantu las,
c. Perlengkapan keselamatan kerja,
d. Elektroda.
A. Pesawat Las
Jika ditinjau dari arus yang ke luar, pesawat las dapat digolongkan menjadi :
1) Pesawat las arus bolak-balik (AC),
2) Pesawat las arus searah (DC),
3) Pesawat las arus bolak-balik dan searah (AC-DC), yang merupakan gabungan dari pesawat AC dan DC.
1) Pesawat Las Arus bBolak-Balik (AC)
Pesawat las jenis ini terdiri dari transformator yang dihubungkan dengan jala PLN atau dengan pembangkit listrik, motor disel, atau motor bensin. Kapasitas trafo biasanya 200 sampai 500 ampere. Sedangkan voltase (tegangan) yang ke luar dari pesawat trafo ini antara 36 sampai 70 volt, dan ini bervariasi menurut pabrik yang mengeluarkan pesawat las trafo ini. Gambar memperlihatkan salah satu jenis pesawat las transformator AC.
2) Pesawat Las Arus Searah (DC)
Pesawat ini dapat berupa pesawat tranformator rectifier, pembangkit listrik motor disel atau motor bensin, maupun pesawat pembangkit listrik yang digerakan oleh motor listrik digerakkan oleh motor listrik (motor generator).
3) Pesawat Las AC-DC
Pesawat las ini merupakan gabungan dari pesawat las arus bolak-balik dan arus searah. Dengan pesawat ini akn lebih banyak kemungkinan pemakainya karena arus yang keluar dapat searah maupun bolak-balik (AC-DC).
Pesawat las jenis ini mialnya tranformator rectifier maupun pembangkit listrik motor disel.
B. Alat-alat bantu Las
Pada pengelasan terdapat alat bantu yang terdiri dari :
1) Kabel las,
2) Pemegang elektroda,
3) Palu las,
4) Sikat kawat,
5) Klem masa,
6) Penjepit.
1. Kabel Las
Kabel las biasanya dibuat dari tembaga yang dipilin dan dibungkus dengan karet isolasi.
Yang disebut kabel las ada tiga macam, yaitu :
a. Kabel elektroda , yaitu kabel yang menghubungkan pesawat las dengan elektroda.
b. Kabel masa, yaitu yang menghubungkan pesawat las dengan benda kerja.
c. Kabel tenaga, yaitu kabel yang menghubungkan sumber tenaga atau jaringan lisrtik dengan pesawat las.
Tabel ukuran kabel las (mm²)
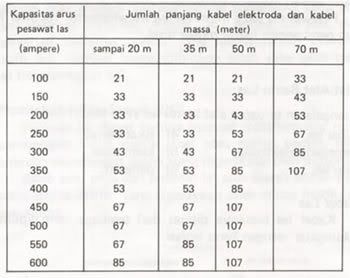
Tabel Ukuran kabel tenaga untuk 3 kabel konduktor
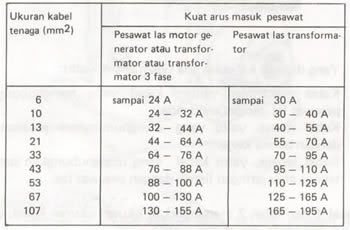
2. Pemegang Elektroda
Ujung yang berselaput dari elektroda dijepit dengan pemegang elektroda. Ini terdiri dari mulut penjepit dan pemegang yang dibungkus oleh bahan penyekat (biasanya dari embonit).
3. Palu Las
Palu ini digunakan untuk melepaskan dan mngeluarkan terak las pada jalur las dengan jalan memukulkan atau menggoreskan pada daerah las. Gunakanlah kaca mata terng pada waktu poembersihan terak, sebeb dapat memercikan pada mata.
4. Sikat Kawat
Sikat kawat digunakan untuk :
a. Membersihkan benda kerja yang akan dilas,
b. Membersihkan terak las yang sudah dilepas dari jalur las oleh pukulan palu las
5. Klem massa
Ini adalah alat untuk menghubungkan kabel masa ke benda kerja. Terbuat dari bahan yang menghantar dengan baik (tembaga). Klem masa dilengkapi dengan pegas yang kuat, yang dapat menjepit benda kerja dengan baik. Tempat yang dijepit harus bersih dari kotoran (karet, cat, minyak dan sebagainya).
6. Penjepit
Ini digubakan untuk memegang atau memindahkan benda kerja yang masih panas sehabis pengelaan.
C. Perlengkapan keselamatan Kerja
Pada perlengkapan keselamatan kerja terdiri dari :
1. Helm las (topeng las),
2. Tarung tangan
3. Baju las (apron)
4. Sepatu las
5. Kamar las
1. Helem Las (Topeng Las)
Gunanya untuk melindungi kulit muka dan mata dari sinar las (ultra violet dan infra merah).
Sinar las yang terang itu tidak boleh dilihat dengan mata langsung sampai jarak 15 meter.Kaca dari helem las atau topeng las adalah khusus yang dapat mengurangi sinar las tersebut. Dan melindungi kaca khusus tersebut dari percikan las, dipakailah kaca kaca bening pada bagian luarnya.
2. Sarung tangan
Dibuat dari kulit atau asbes lunak. Untuk memudahkan memegang pemegang elektroda. Pada waktu mengelas, sarung tangan ini selalu harus dipakai.
3. Baju Las (Apron)
Dibuat dari kulit atau asbes. Baju las yang lengkap dapat melindungi badan dan sebagaian kaki.
Untuk pengelasan posisi di atas kepala harus memakai baju las yang lengkap. Sedangkan pengelasan lainya cukup menggunakan apron.
4. Sepatu Las
Berguna untuk melindungi kaki dari semburan bunga api. Jika tidak ada sepatu las, pakailah sepatu biasa yang rapat, jangan sampai mudah kemasukan percikan bunga api.
5. Kamar Las
Kamar las dibuat dari bahan tahan api. Kamar las penting, yaitu agar orang yang ada di sekitar tidak terganggu oleh bahaya las.
Untuk mengeluarkan gas, sebaiknya kamar las dilengkapi dengan sistem ventilasi. Kamaar las dilengkapi dengan meja las yang bebas dari bahaya kebakaran. Di sekitar kamar las ditempatkan alat pemadam kebakaran dan pasir.
D. Elektroda
Elektroda yang dipergunakan pad alas busur mempunyai perbedaan komposisi selaput maupun kawat inti. Diantaranya adalah elektroda berselaput .
Pada elektroda ini pengelasan fluksi pada kawat inti dapat dengan cara destruksi, semprot atau celup.
Ukuran standar diameter kawat inti dari 1,5 sampai 7 mm dengan panjang antara 350 sampai 450 mm.
1. Jenis – jenis Selaput Fluksi Elektroda
Bahan untuk selaput fluksi elektroda tergantung pada kegunaanya, yaitu antara lain selulosa, kalium karbonat, tintanikum dioksida, kaolin, kalium oksida mangan, oksida besi, serbuk besi, besi silicon, besi mangan dan sebagainya, dengan persentase yang berbeda-beda untuk tiap jenis elektroda.
2. Tebal selaput
Tergantung dari jenisnya, tebal selaput elektroda antara 10% sampai 50% dari diameter elektroda.
Pada waktu pengelasan selaput elektroda ini nakan ikut mencair dan menghasilkan gas CO2 yang melindungi cairan las, busur listrik, dan sebagian benda kerja terhadap udara luar.
Udara luar yang mengandunng O2 dan N akan dapat mempengaruhi sifat mekanik dari logam las. Cairan selaput yang disebut terak akan tereapung dadn membeku melapisi permukaan las yang masih panas.
Memilih Besar Arus Listrik
Besarnya arus listrik untuk pengelasan tergantung pada ukuran diameter dan macam-macam elektroda las.
Tabel Besar arus dalam ampere dan diameter (mm)
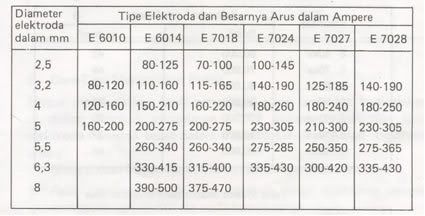
Keterangan :
a. E menyatakan elektroda
b. Dua angka setelah E (misalnya 60 atau 70) menyatakan kekuatan tarik defosit las dalam ribuan dengan 1b/inchi²
c. Angka ketiga setelah E menyatakan posisi pengelasan, yaitu :
- Angka (1) untuk pengelasan segala posisi,
- Angka (2) untuk pengelasan posisi datar dan bawah tangan.
d. Angka ke empat setelah E menyatakan jenis selaput dan jenis arus yang cocok dipakai untuk pengelasan.
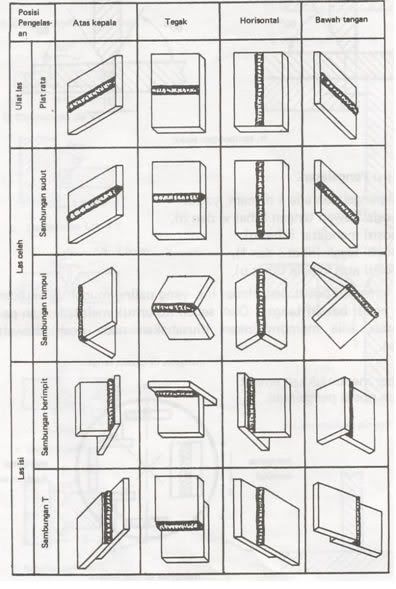
Dasar- dasar Las Gas
Las gas, yang dilapangann lebih dikenal dengan istilah las karbit, sebenarnya adalah pengelasan yang dilaksanakan dengan pencampuran 2 jenis gas sebagai pembentuk nyala api dan sebagai sumber panas. Dalam proses las gas ini, gas yang digunakan adalah campuran dari gasa Oksigen (O2) dan gas lain sebagai gas bahan bakar (fuel gas). Gas bahan bakar yang paling popular dan paling banyak digunakan dibengkel-bengkel adalah gas Aetilen ( dari kata “acetylene”, dan memiliki rumus kimia C2H2 ). Gas ini nmemiliki beberapa kelebihan dibandingkan gas bahan bakar lain. Kelebihan yang dimiliki gas Asetilen antara lain menghasilkan temperature nyala api lebih tinggi dari gas bahan bakar lainya, baik bila dicampur dengan udara ataupun Oksigen.
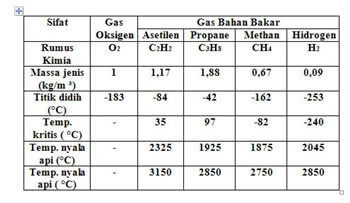
Dari table diatas, gas-gas lain yang juga berperan adalah gas propane (LPG), methane dan hydrogen. Karena temperature nyala api yang dihasilkan lebih rendah dari gas asitilen maka ketiga jenis gas ini jarang dipakai sebagai gas pencampur.
Seperti disebut diatas, gas Asetilen merupakan jenis gas yang paling banyak digunakan sebagi bpencampuran dengan gas Oksigen. Jika gas Asetilen digunakan sebagi gas pencampur maka seringkali proses pengelasan disebut dengan las karbit. Gas Asetilen ini sebenarnya dihasilkan dari reaksi batu Kalsium KARBIDA (orang-orang menyebut karbit). Dengan air. Jadi jika Kalsium Karbida ini disiram atau dicelupkan ke dalam air maka akan terbentuk gas Asetilen. Jadi penyebutan nama las karbit hanya untuk mencirikan bahwa gas yang digunakan salah satunya adalah gas Asetilen.
Selain dikenal dengan nama las karbit, kadang-kadang masyarakat umum menyebut kan juga dengan nama lain yaitu las MDQ. Penyebutan nama MDQ ini sesungguhnya mengacu pada satu merk batu karbit. Jadi nama las karbit atau las asetilen atau las MDQ sebenarnya adalah satu nama proses las yan sama.
Untuk dapat melakukan pengelasan dengan car alas gas, diperlukan peralatan seperti tabung gas Oksigen dan tabung gas Asetilen, katup tabung, regulator (pengatur tekana gas), selang gas dan torch (brander). Kedua gas Oksigen dan Asetilen keluar dari masing-masing tabung dengan tekanna tertentu, mengalir menuju torch melalui regulator dan selang gas. Setelah sampai di torch kedua gas tercampur dan akhirnya keluar dari ujung nosel torch. Dengan bantuan pematik api, campuran gas yang keluar dari ujung nosel membentuk nyala api denagn intensitas tertentu
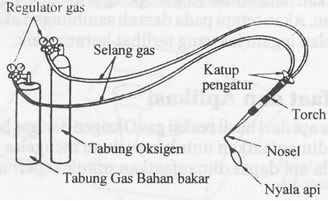
Peralatan dalam Proses Las Gas
Proses las gas (dibuku ini akan sering disebutkan las gas untuk mencirikan bahwa las yang dimaksud adalah las yang melibatkann campuran gas Oksigen dan gas bahan bakar) umumnya dipakai secar manual yaitu dikerjakan oleh tangan juru las. Pengaturan panas dan pemberian kawat las dilakukan oleh kombinasi kedua tangan juru las. Oleh karena itu, kualitas sambungan nantinya akan diperngaruhi oleh ketrampilan dan keahlian si juru las.
Sebenarnya suadah ada pengembangan dari proses las gas ini menjadi semi-otomatis atau “dimensikan”. Tentu saja hal itu dilaarbelakangi oleh keinginan untuk mendapatkan kualitas ambungan yang lebih baik. Dengan system yang sudah otomatis maka pengaturan panas dan pemberian kawat las akan lebih baik lagi. Kebanyakan otomatis system diterapkan apada operasi-operai pemotongan pelat logam dimana pada sitem itu kecepatan pemotongn dapat diatur.
Proses las gas dapat dilaksanakan dengan pemberian kawat las (atau istilah logam pengisi) atau tidak sama sekali. Satu syarat dimana diperlukan logam pengisi atau tidak adalah dilihat dari ketebalan pelat yang akan di las. Jika pelat itu tipis maka untuk menyambungnya dapat dilakukan tanpa memberikan logam pengisi, sedangkan untuk pelat-pelat tebal diperlukan logam pengisi untuk menjamin sambungan yang optimal. Jika pada pelat tipis dipaksakan harus diberi logam pengisi maka hal itu mungkin saja dilakukan. Akan tetapi pada daerah sambungan akan nampak tonjolan logam las yang terlihat kurang baik.
Nyala api dari hasil reaksi gas Oksigen dan gas bahan bakar tidak hanya dimanfaatkan untuk keperluan mengelas saja. Lebih dari itu, nyala api dapat dimanfaatkan untuk keperluan lainnya, seperti :
1. Operasi branzing ( flame brazing )
Yang dimaksud dengan branzing disini adalah proses penyambunngan tanpa mencairkan logam induk yang disambung, hanya logam pengisi saja. Misalnya saja proses penyambungan pelat baja yang menggunakan kawat las dari kuningan. Ingat bahwa titik cair Baja ( ± 1550 °C) lebih tinggi dari kuningan ( sekitar 1080°C). dengan perbedaan titik car itu, proses branzing, akan lebih mudah dilaksanakan daripada proses pengelasan.
2. Operasi pemotongan logam ( flame cutting )
Kasus pemotongan logam sebenarnya dapat dilakukan dengan berbagai cara. Proses penggergajian (sewing) dan menggunting (shearing) merupakan contoh dari proses pemotongan logam dan lembaran logam.
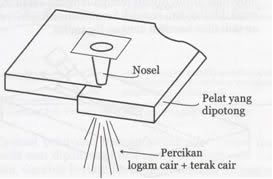
Operasi Pemotong Pelat Logam
Proses menggunting hanya cocok diterapkan pada lembaran logam yang ketebalannya tipis. Proses penggergajian dapat diterapkan pada pelat yang lebih tebal tetapi memerlukan waktu pemotongan yang lebih lama. Untuk dapat memotong pelat tebal denngan waktu lebih singkat dari cara gergaji maka digunakan las gas ini denngan peralatan khusus misalnya mengganti torch nya ( dibengkel-bengkel menyebutnya brender ).
Pemotongan pelat logam dengan nyala api ini dilakukan dengan memberikan suplai gas Oksigen berlebih. Pemberian gas Oksigen lebih, dapat diatur pada torch yang memang dibuat untuk keperluan memotong.
3. Operasi perluasan / pencukilan (flame gauging)
Operasi perluasan dan pencukilan ini biasanya diterapkan pada produk/komponen logam yang terdapat cacat/retak permukaannya. Retak/cacat tadi sebelum ditambal kembali dengan pengelasan, terlebih dahulu dicukil atau diperluas untuk tujuan menghilangkan retak itu. Setelah retak dihilangkan barulah kemudian alur hasil pencungkilan tadi diisi kembali dengan logam las.
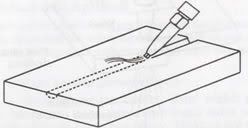
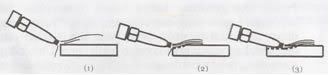
4. Operasi pelurusan (flame straightening)
Operasi pelurusan dilaksanakan dengan memberikan panas pada komponen dengan bentuk pola pemanasan tertentu. Ilustrasi dibawah ini menunjukkan prinsip dasar pemuaian dan pengkerutan pada suatu logam batang.
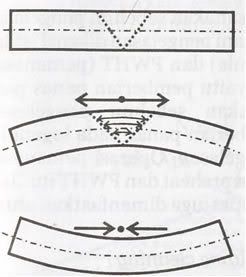
Batang lurus dipanaskan dengan pola pemanasan segitiga
Logam cenderung memuai pada saat dipanaskan. Daerah pemanasan tersebut menghasilkan pemuaian yang besar.
Logam mengkerut pasa saat didinginkan. Daerah pemanasan terbesar menghasilkan pengkerutan yang besar pula.
Prinsip Pemuaian dan Pengkerutan Logam
Las Gas Asetilen
A. Peralatan
Untuk dapat mengelas atau memotong ataupun fungsi lainya dari proses las gas maka diperlukan peralatan yang dapat menunjang fungsi-fungsi itu. Secara umum, peralatan yang digunakan dalam gas iniadalah :
1. Tabung gas Oksigen dan tabung gas bahan bakar,
2. Katup silinder/tabung,
3. Regulator,
4. Selang gas,
5. Torch,
6. Peralatan pengaman
1. Tabung Gas
Tabung gas berfungsi untuk menampung gas atau gas cair dalam kondisi bertekanan. Umumnya tabung gas dibuat dari Baja, tetapi sekarang ini sudah banyak tabung-tabung gas yang terbuat dari paduan Alumunium. Tabung gas tersedia dalam bentuk beragam mulai berukuran kecil hingga besar. Ukuran tabung ini dibuat berbeda karena disesuaikan dengan kapasitas daya tampung gas dan juga jenis gas yang ditampung.
Untuk membedakan tabung gas apakah didalamnya berisi gas Oksigen, Asetilen atau gas lainya dapat dilihat dari kode warna yang ada pada tabung itu. Table berikut ini menunjukan kode warna tabung gas untuk berbagai jenis warna.
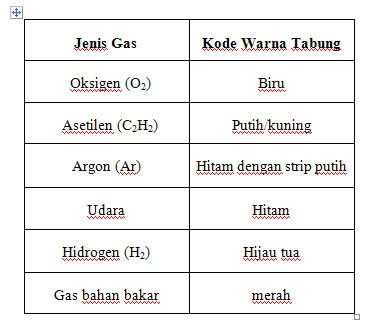
2. Katup Tabung
Sedang pengatur keluarnya gas dari dalam tabung maka digunakan katup. Katup ini ditempatkan tepat dibagian atas dari tabung. Pada tabung gas Oksigen, katup biasanya dibuat dari material Kuningan, sedangkan untuk tabung gas Asetilen, katup ini terbuat dari material Baja.
3. Regulator
Regulator atau lebih tepat dikatakan Katup Penutun Tekan, dipasang pada katub tabung dengan tujuan untuk mengurangi atau menurunkan tekann hingga mencapai tekana kerja torch. Regulator ini juga berperan untuk mempertahankan besarnya tekanan kerja selama proses pengelasan atau pemotongan. Bahkan jika tekanan dalam tabung menurun, tekana kerja harus dipertahankan tetap oleh regulator.
Pada regulator terdapat bagian-bagian seperti saluran masuk, katup pengaturan tekan kerja, katup pengaman, alat pengukuran tekanan tabung, alat pengukuran tekanan kerja dan katup pengatur keluar gas menuju selang.
4. Selang Gas
Untuk mengalirkan gas yang keluar dari tabung menuju torch digunakan selang gas. Untuk memenuhi persyaratan keamanan, selang harus mampu menahan tekan kerja dan tidak mudah bocor. Dalam pemakaiannya, selang dibedakan berdasarkan jenis gas yang dialirkan. Untuk memudahkan bagimana membedakan selang Oksigen dan selang Asetilen mak cukup memperhatikan kode warna pada selang. Berikut ini diperlihatkan table yang berisi informasi tentang perbedaan warna untuk membedakan jenis gas yang mengalir dalam selang.
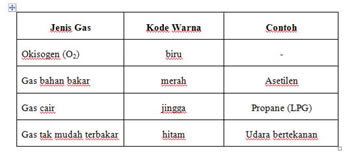
Torch
Gas yang dialirkan melalui selang selanjutnya diteruskan oleh torch, tercampur didalamnya dan akhirnya pada ujuang nosel terbentuk nyala api. Dari keterangan diatas, toch memiliki dua fungsi yaitu :
a. Sebagai pencampur gas oksigen dan gas bahan bakar.
b. Sebagai pembentuk nyala api diujung nosel.
Torch dapat dapat dibagi menjadi beberapa jenis menurut klasifikasi berikut ini :
1. Menurut cara/jalannya gas masuk keruang pencampur.
Dibedakan atas :
Injector torch (tekanan rendah)
Pada torch jenis ini, tekanan gas bahan bakar selalu dibuat lebih rendah dari tekanan gas oksigen.
Equal pressure torch (torch bertekanan sama)
Pada torch ini, tekanan gas oksigen dan tekanan gas bahan bakar pada sisi saluran masuk sama besar.proses pencampuran kedua gas dalam ruang pencampur berlangsung dalam tekanan yang sama.
2. Menurut ukuran dan berat. Dibedakan atas :
- Toch normal
- Torch ringan/kecil
3. Menurut jumlah saluran nyala api. Dibedakan atas :
- Torch nyala api tunggal
- Torch nyala api jamak
4. Menurut gas yang digunakan. Dibedakan atas :
- Torch untuk gas asetilen
- Torch untuk gas hydrogen, dan lain-lain.
5. Menurut aplikasi. Dibedakan atas :
- Torch manual
- Torch otomatik/semi otomatik.
6 comments:
salam,bagus sekali postingannya, terimakasih banyak mas Dendi....jazakaalahkhoir... dan selamat berkarya ..
bisa ndk mengelas plat 1 mm scara halus
Bagus sekali posting anda di blog ini sangat membantu sekali
kalo peraalatan las asetilin harga lengkapnya berapa
Bisa acetylene diganti dengan prophane utk torch welding...?
Klo las mig arusnya ter balik gmna?
Post a Comment